Headstock
The main function of the Headstock is to house the Spindle and its bearings.
The Spindle is machined from a piece of 45mm O.D. hollow bar, having a 25mm I.D.
Separate oil seal collars are also machined, allowing the collars to be replaced if required.
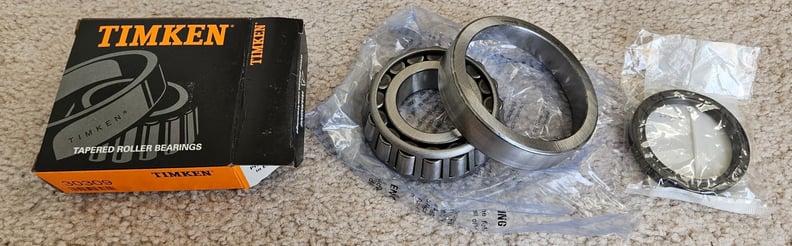
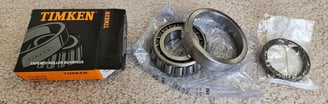
We will send you a free copy of these Lathe Design Notes (PDF file)
by entering your Name and Email below ...or you can visit the My Store pages and download from there ...
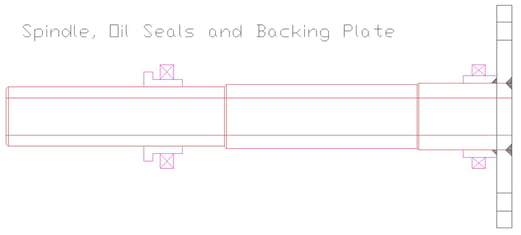
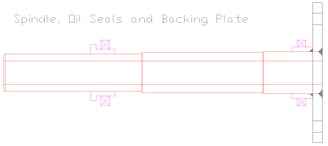
Quality tapered roller bearings are used, and the presence of the oil seals allows the bearings to run in a bath of oil. A feature not readily seen in other homemade lathes.
Laser-cut rings of varying diameters and thicknesses make up the bearing and oil seal housings.
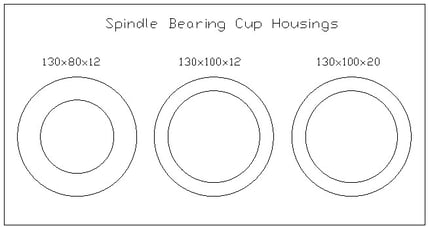
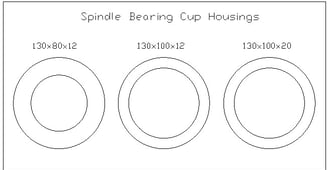
Regarding bearing alignment, most DIY lathes seen either have substandard ball bearings in self-aligning housings (read vibrations) or tend to have tapered bearing housings bolted to each end of a heavy welded metal box (read misalignment) and no oil seals (read bearing failure). There is no way that the two mounting faces of the ‘headstock box’ are parallel after welding or even bolting.
Another major design feature of the Hi Lo Metal Lathe is the bearing alignment process that allows for accurate DIY alignment.
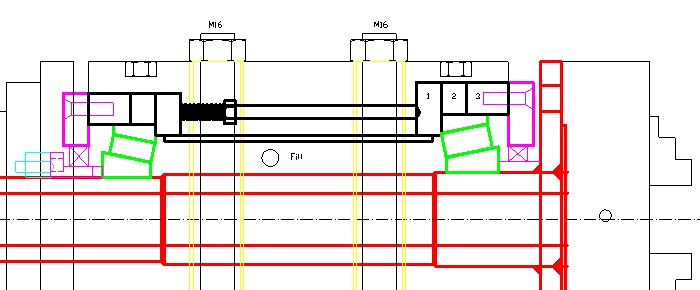
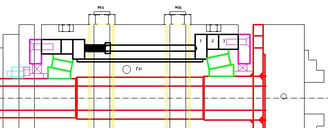
Each bearing housing for the tapered roller bearings is made up of 3 laser cut rings. No machining will be necessary to achieve perfect front and back bearing alignment.
Rings 2 and 3 will be cut slightly larger than the diameter of the outside bearing cup. The bearing cup is glued into ring 2 using ‘epoxy steel paste’. Ring 1 is then epoxied to ring 2. Ring 3 is then epoxied to ring 2 using the bearing cup for alignment. The Spindle is then fitted up with the bearings and the bearings are given some pretension, against 3 spring loaded alignment rods.
This setup will ensure that the bearing housings will position themselves into precise alignment.
The ‘ring’ components are simply included in the laser cutting schedule, and this arrangement avoids any machining requirements and the need to acquire large round stock for the housings.
Once satisfied with the bearing alignment, the whole assembly, including Headstock bolt tubes and base plates, is placed into a box mould and filled with the epoxy granite mixture.
The Headstock is bolted to the Base using 4 x 16mm bolts. The use of shims and lateral adjustment screws ensures that the axis of the Spindle can be perfectly aligned parallel to the Ways.
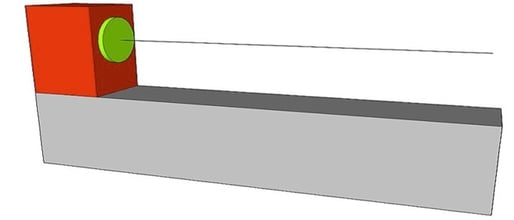
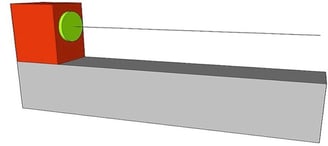
One end of the Spindle is fitted with the chuck backing plate and is also bored out to a Morse #4 taper to allow the use of centres, etc. The other end of the Spindle will carry a four-step v-belt pulley, a bearing tensioner collar, an optional gear for dividing and/or feed screw drive, and space for a centering spider.
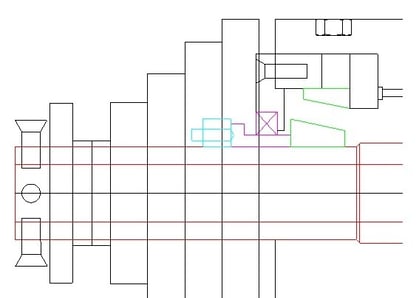
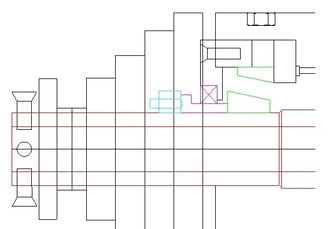
The Spindle will be machined on the ‘wood lathe setup’. In lieu of that, a temporary Spindle in self-aligning bearings could be set up on the Ways, and the purchased X-Y table can be used, or these parts could be machined elsewhere. Note that a ‘press fit’ is all that is required on the Spindle and that surface finish is not critical.
Again, the use of epoxy granite as the main Headstock material allows precision alignment, along with good mass and vibration dampening characteristics.
Hi Lo Metal Lathe
Build your own metal lathe
Enquiries
info@hilometallathe.com
© 2024. All rights reserved.